Sommaire
Dans un monde industriel de plus en plus connecté, la robustesse et la fiabilité des réseaux sont primordiales pour assurer une productivité constante et éviter des pertes économiques considérables. Les défaillances réseau peuvent survenir à tout moment, entraînant des interruptions de service et des retards de production. Réparer efficacement ces réseaux endommagés est une opération délicate qui nécessite une expertise technique, une planification méthodique et une exécution rapide. Cet article vise à éclairer les professionnels sur les étapes fondamentales à suivre pour remettre en état leurs systèmes de réseaux industriels. De la préparation initiale à la remise en service, chaque phase sera décortiquée pour vous permettre de comprendre l'ampleur de la tâche et les meilleures pratiques à adopter. Embarquez dans ce parcours instructif et découvrez comment transformer une situation critique en un succès retentissant pour votre infrastructure réseau.
Identification des causes et diagnostic
Avant de procéder à la réparation d'un réseau industriel, la détermination des éléments déclencheurs de la défaillance est une phase incontournable. Cette analyse minutieuse permettra de cibler les interventions et d'optimiser les processus de remise en état. Il s'agit d'étudier les signaux d'erreur émis, de consulter les rapports de fonctionnement et d'effectuer des tests de diagnostic approfondis. Dans ce cadre, la maîtrise du protocole de communication industriel est requise pour comprendre les échanges d'informations au sein du réseau et pour détecter les anomalies spécifiques. L'accent doit également être mis sur la maintenance préventive, car une compréhension détaillée des incidents permet de prévenir de futurs dysfonctionnements. Tout ingénieur spécialisé en systèmes de réseautique industrielle saura que la réussite de la réparation d'un réseau passe par une excellente connaissance des mécanismes de diagnostic réseau, de l'analyse d'erreurs et mettra en œuvre son expertise pour assurer la durabilité des solutions appliquées.
Planification de la réparation et des mesures préventives
La réussite de la réparation des réseaux industriels endommagés dépend en grande partie d'une planification rigoureuse. Après avoir identifié les causes de la défaillance, il est essentiel de choisir avec précision le matériel de remplacement adapté, de définir minutieusement les procédures de sécurité et d'arrêter un calendrier d'intervention détaillé. Ce processus nécessite souvent des compétences spécifiques, typiquement celles d'un responsable de la maintenance industrielle. Il est aussi recommandé d'utiliser un système de gestion de la maintenance assistée par ordinateur (GMAO), qui permet de planifier et de suivre les interventions de manière efficace.
Les mesures préventives jouent également un rôle prépondérant dans la pérennité des réseaux. Elles consistent à mettre en place des procédures qui anticipent les possibles défaillances et permettent d'agir rapidement avant que les dommages ne s'aggravent. L'expertise d'une entreprise spécialisée comme Aquitaine Réseaux Tuyauterie, reconnue pour son savoir-faire en assemblage et pré-montage pour réseaux industriels, peut s'avérer une ressource inestimable dans la mise en œuvre de ces solutions clés en main.
En somme, la planification de la réparation et l'application de mesures préventives constituent un ensemble de démarches stratégiques pour restaurer et maintenir les réseaux industriels en bon état de fonctionnement. L'implication de professionnels qualifiés et l'utilisation d'outils technologiques adaptés sont des facteurs déterminants pour l'efficacité et la sécurité des opérations de maintenance.
Mise en œuvre des réparations
L'élaboration d'une mise en œuvre efficace est déterminante dans le processus de réparation réseau. Cette phase doit s'appuyer sur une planification rigoureuse et une intervention technique adéquate. Le respect de la norme de sécurité électrique industrielle est impératif pour garantir la protection des travailleurs et la pérennité des équipements. Chaque action doit concourir à la maintenance industrielle de manière à rétablir la fiabilité du réseau. La minutie et la compétence des techniciens sont prépondérantes pour assurer une remise en service sans faille des systèmes affectés.
Tests de fonctionnement et validation
Une fois la réparation des réseaux industriels accomplie, il convient d'opérer des tests de validation rigoureux pour confirmer le bon fonctionnement de l'ensemble. La performance réseau après intervention dépend de l'efficacité de ces tests qui sont un gage de fiabilité pour l'entreprise. Dans le domaine de la sécurité industrielle, il n'y a pas de place pour l'approximation; le contrôle qualité doit être mené avec la plus grande précision pour détecter toute anomalie pouvant affecter le bon déroulement des opérations industrielles.
La procédure de test de charge est un élément technique essentiel dans ce processus. Elle consiste à simuler une situation de fonctionnement à pleine capacité pour vérifier la tenue et la réactivité du réseau sous des conditions extrêmes. Le redémarrage du système est également un moment déterminant où l'on doit observer la réaction du réseau face à la mise en marche soudaine des équipements. Seul un ingénieur en contrôle de qualité, avec son expertise technique et sa connaissance approfondie des normes en vigueur, sera en mesure de développer et d'appliquer un protocole de tests adapté aux spécificités du réseau industriel concerné.
Rétablissement complet et suivi post-réparation
Le rétablissement complet du réseau et le suivi post-réparation marquent l'ultime phase dans la gestion des réseaux industriels après un incident. Ces actions garantissent la fiabilité à long terme du système réparé. Ce processus implique une surveillance de réseau minutieuse, permettant de détecter les moindres anomalies qui pourraient indiquer des défaillances imminentes. L'intégration de stratégies prédictives, telles que la maintenance prédictive, joue un rôle primordial dans cette optique. Ces méthodes utilisent des données et des analyses statistiques pour prévoir les pannes avant qu'elles ne surviennent, permettant ainsi de planifier les interventions en amont et de réduire les temps d'arrêt. Le suivi post-réparation est un gage de pérennité et d'optimisation des performances du réseau industriel.
Sur le même sujet
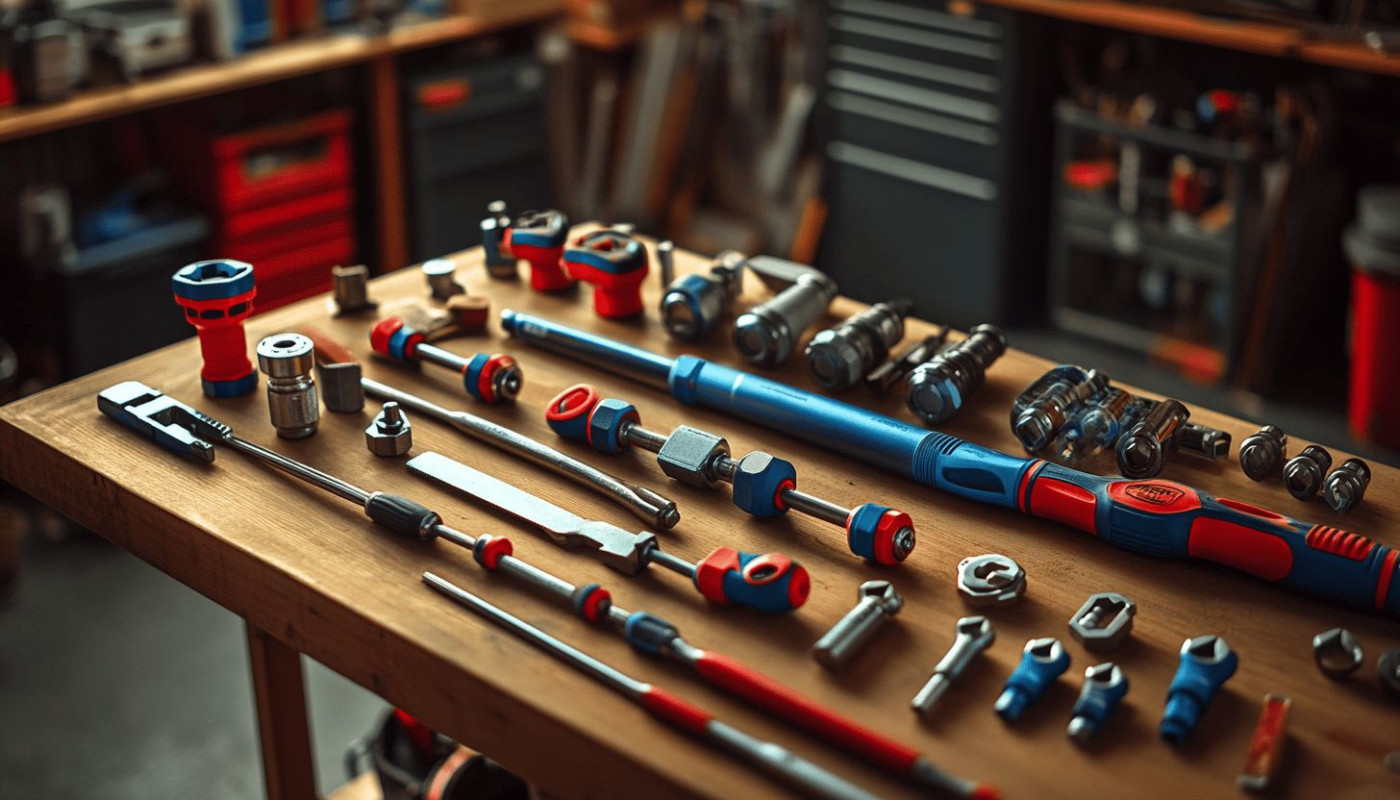
Maximiser confort et sécurité : le rôle crucial de la plomberie et de la serrurerie
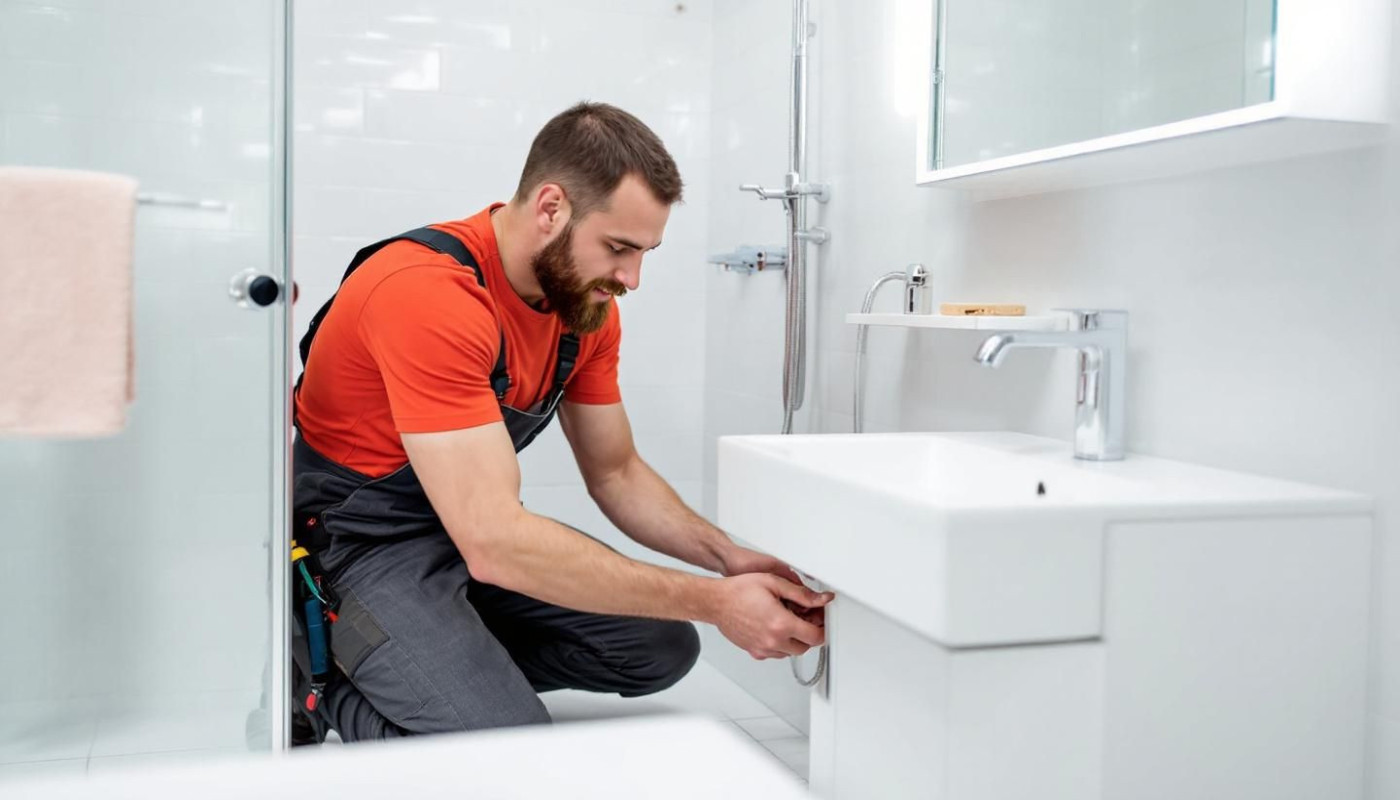
Maximiser la longévité de vos installations sanitaires : méthodes et avantages
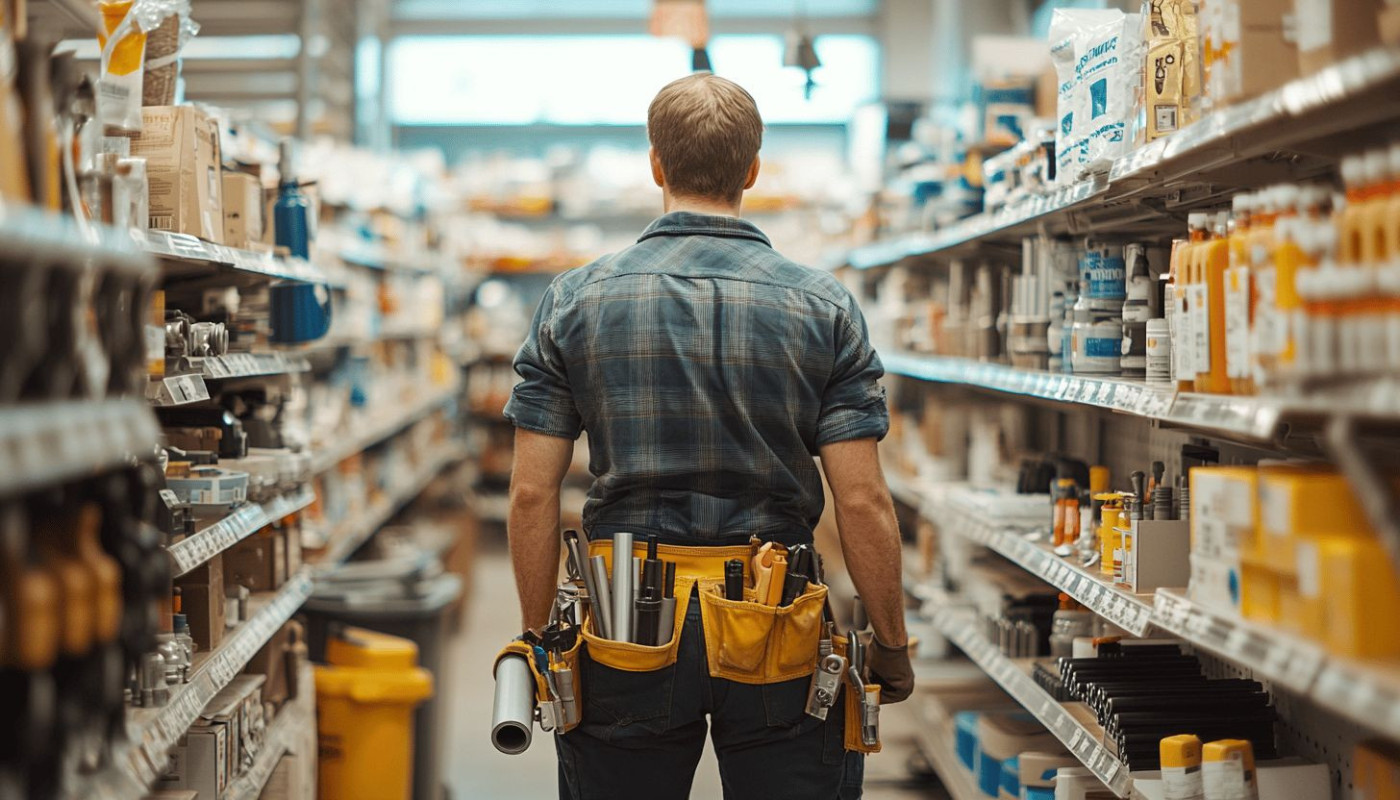
Guide complet pour choisir le bon service de dépannage sanitaire
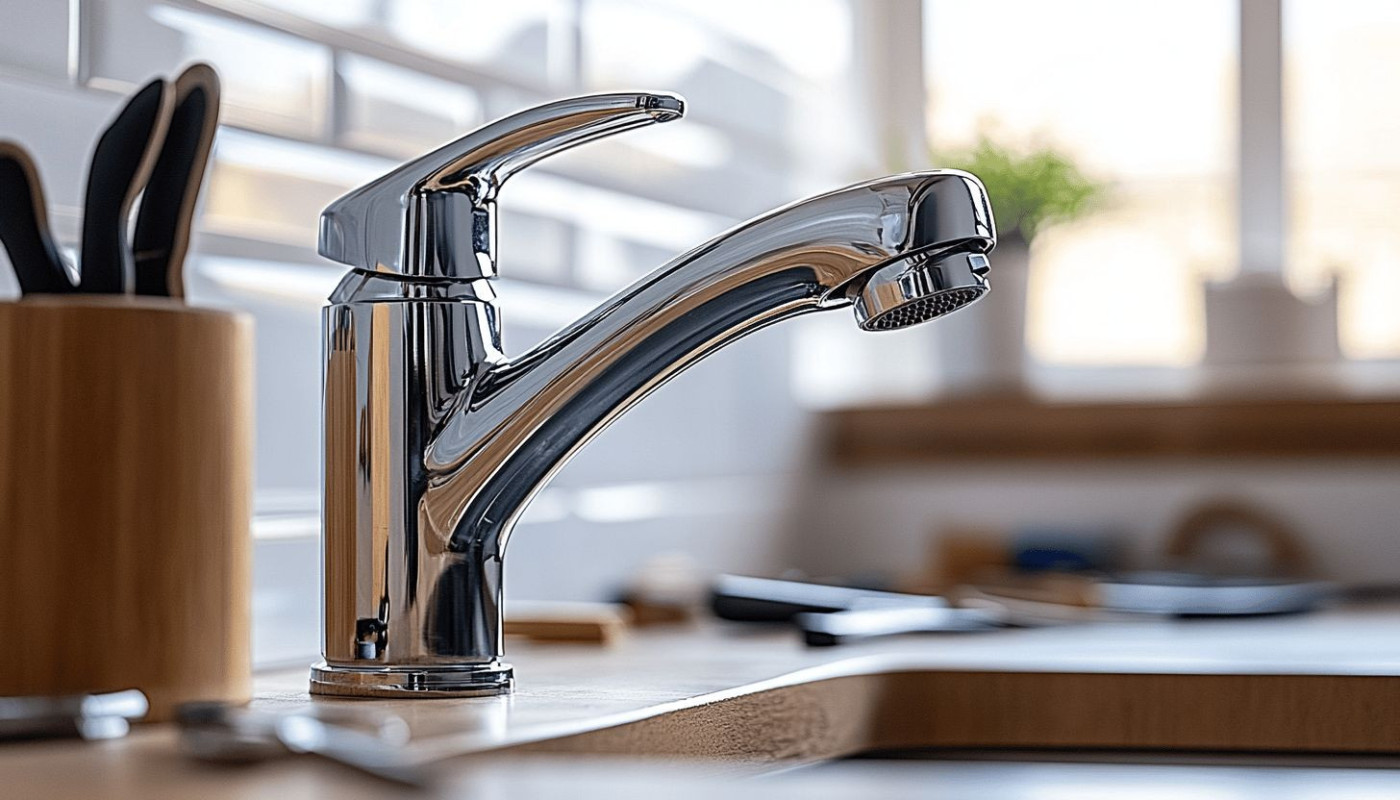
Remplacement d'un robinet comment choisir le bon modèle et l'installer sans faille
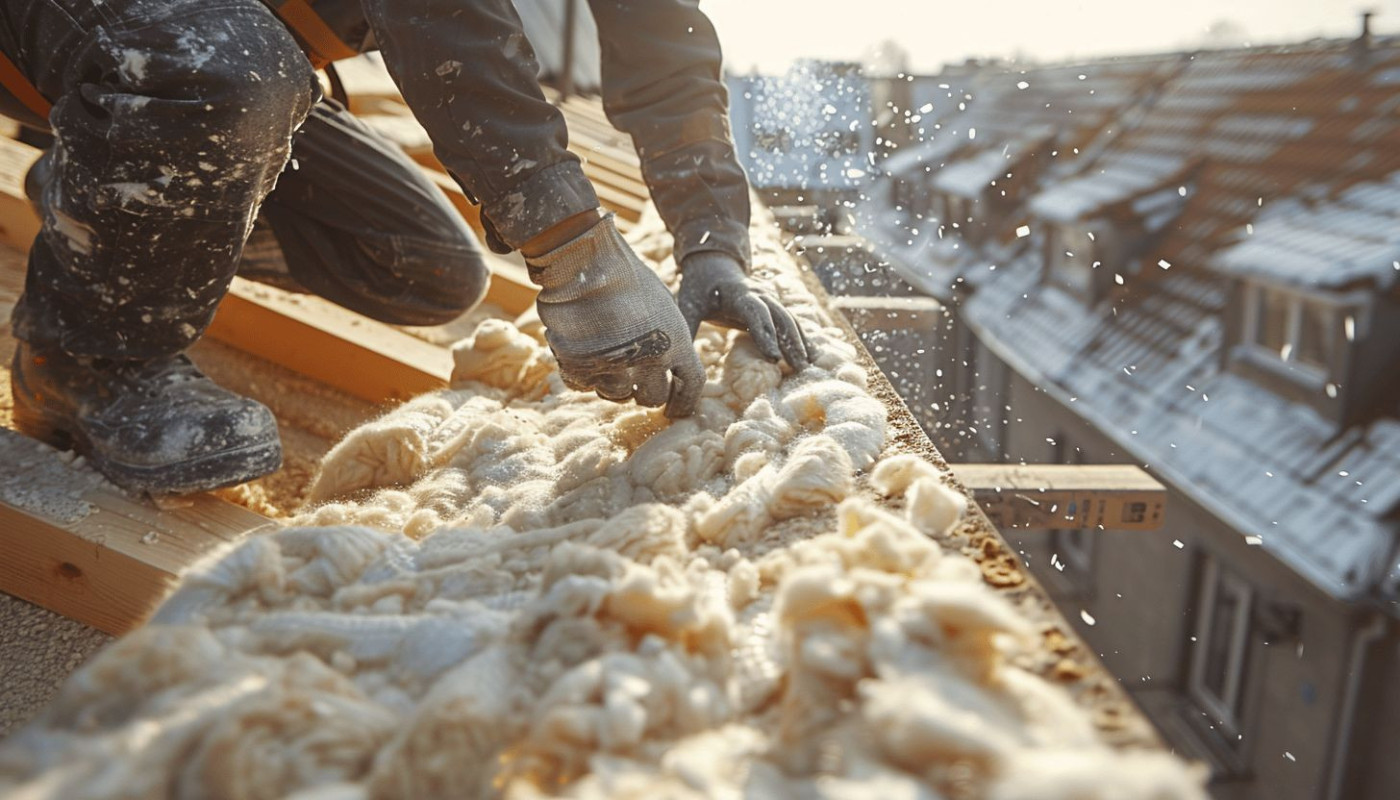
Isolation thermique par l'extérieur matériaux écologiques et méthodes
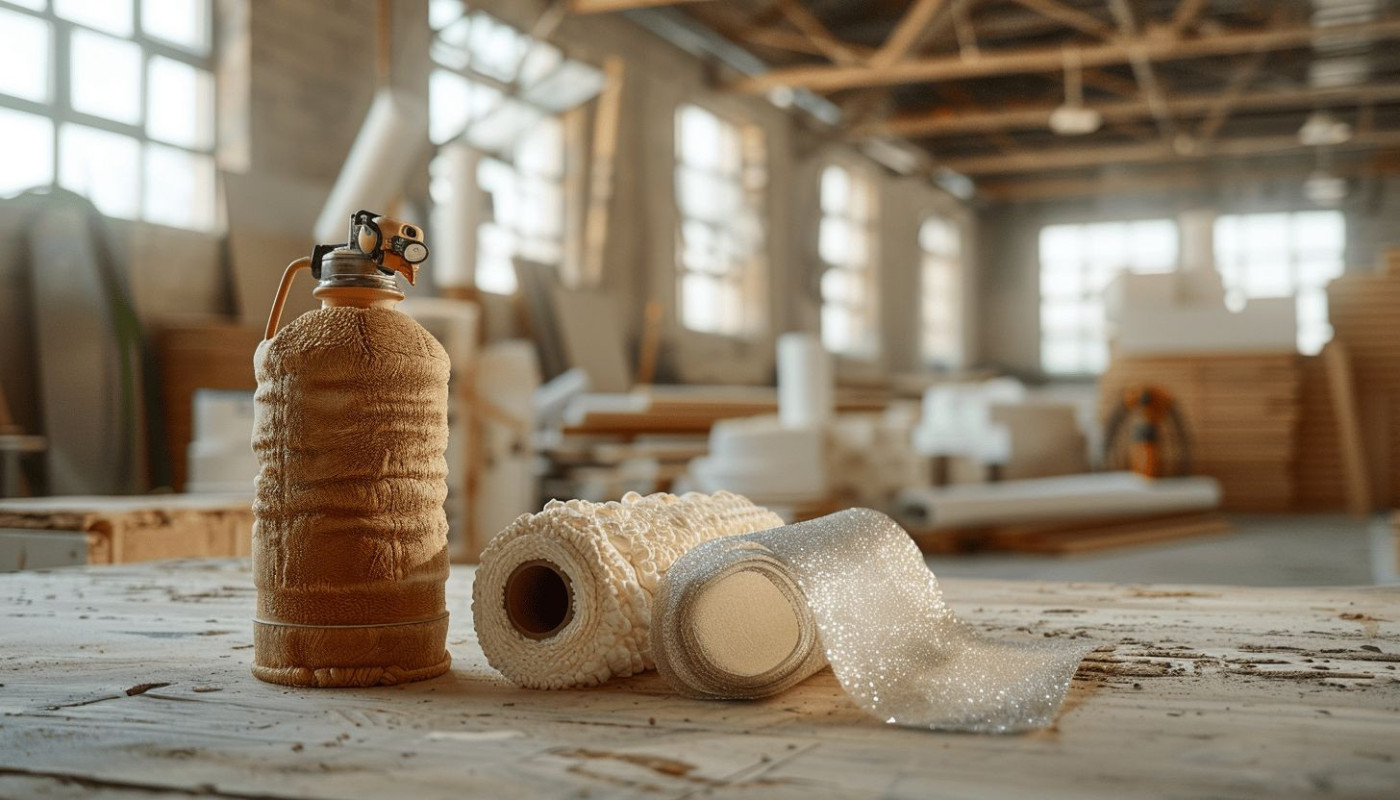
Comment choisir entre la mousse projetée et la laine de verre pour votre isolation
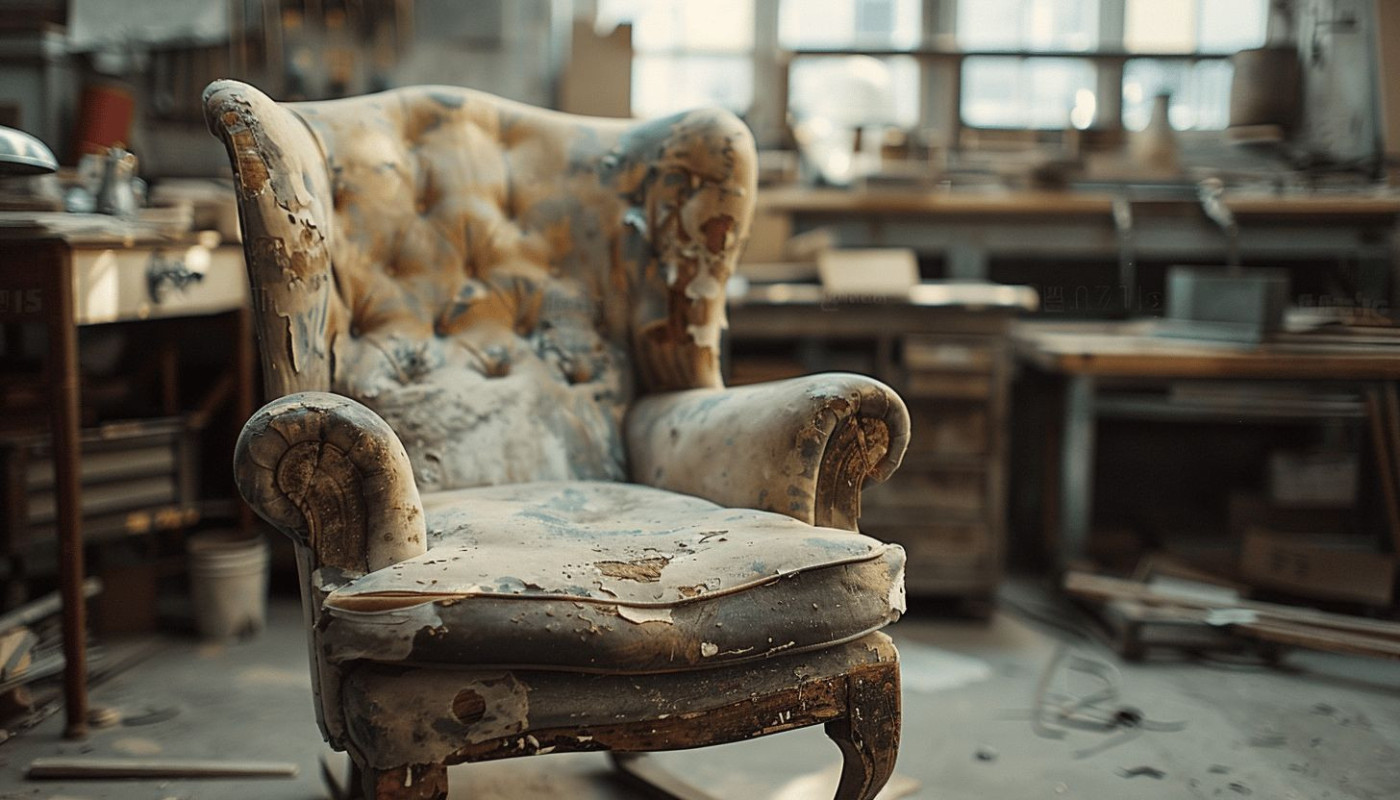
L'art de restaurer une chaise vintage étapes et conseils pour un résultat professionnel
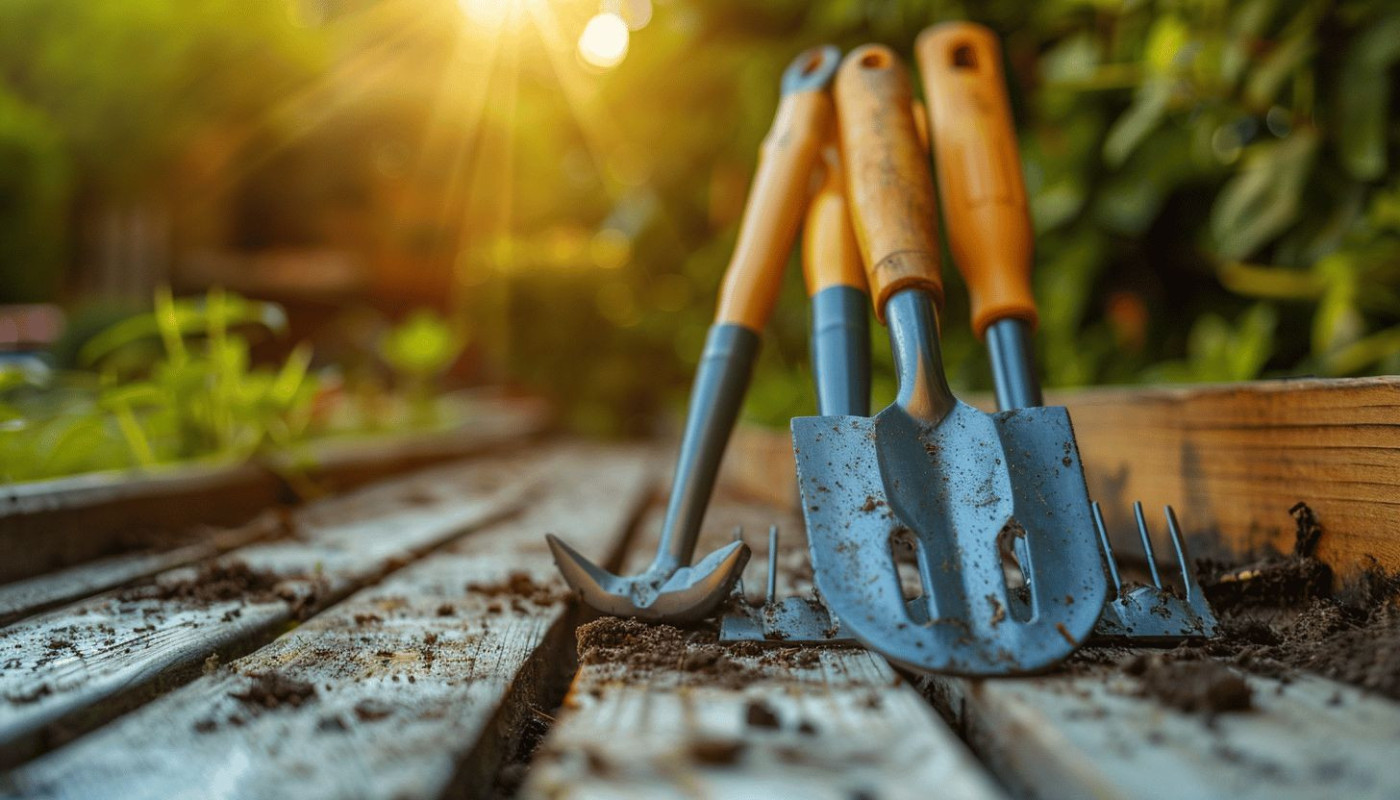
Prévention de la rouille sur les outils de jardinage comment réparer et entretenir
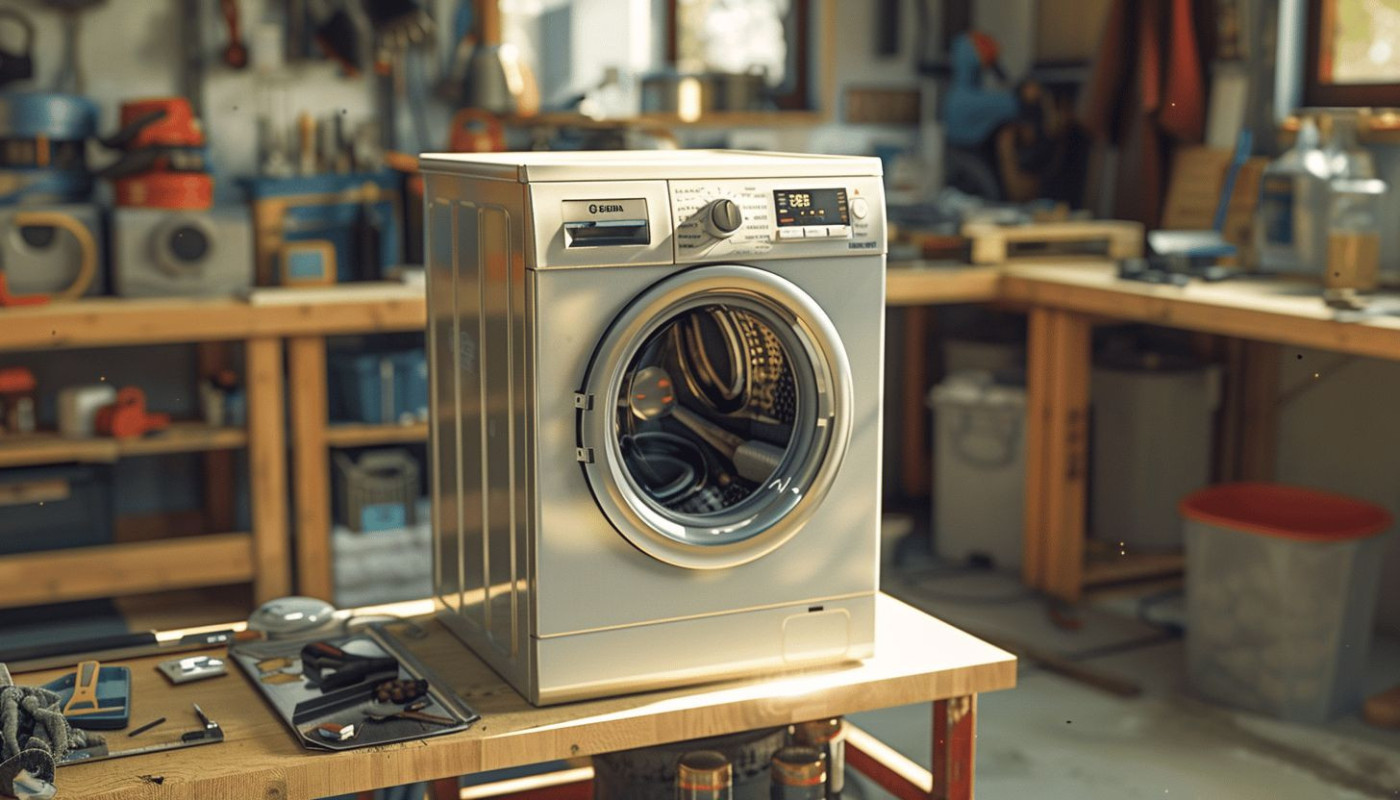
Réparer ou remplacer évaluation des coûts pour appareils ménagers endommagés
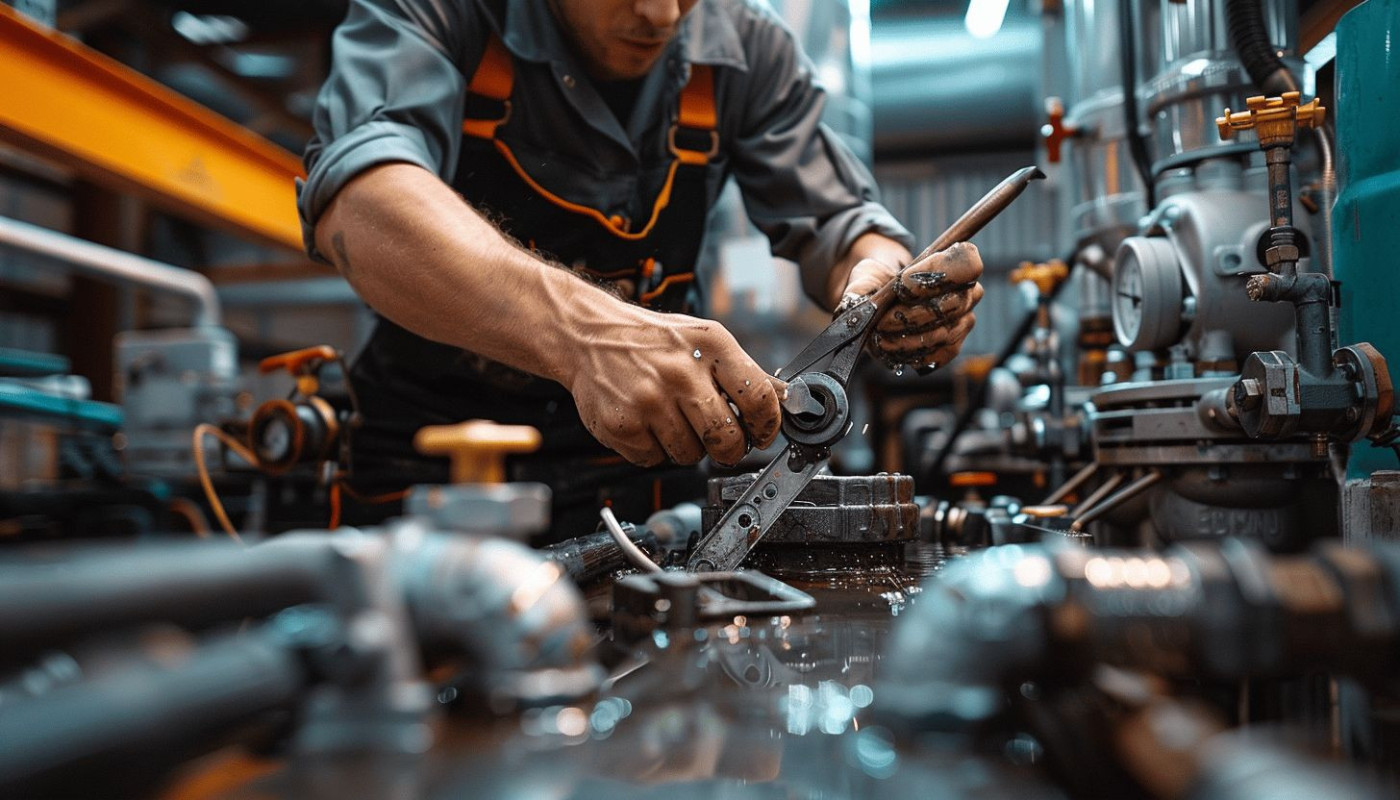